How TPM (Total Productive Maintenance) helps in Lean Production?
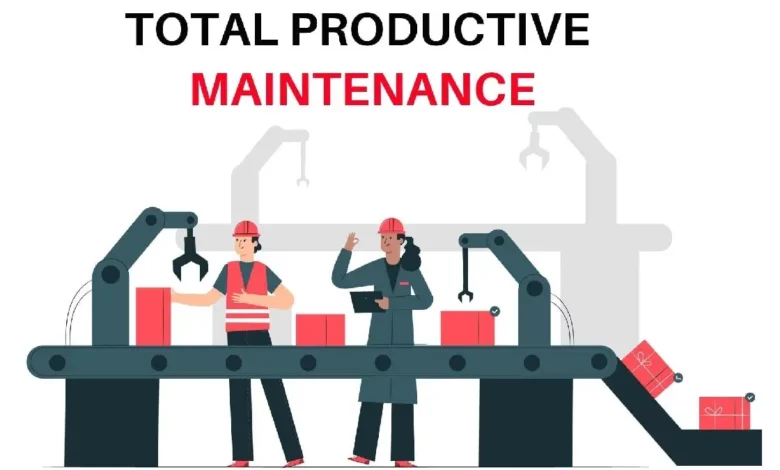
Over the last few years, “lean production objectives” have become a major concern for industries and production professionals. We have plenty of methods for this goal but a major and credible methodology that helps lean production in TPM. Under the quality management category, production specialists can complete Green Belt Training to learn the DMAIC methodology to understand the TPM approach. Understanding the real meaning of Total Productive Maintenance is more important than checking the benefits of this idea in physical asset management.
Frequently breakdowns are one of the major hurdles for the manufacturing firm. Accidents, defects, and mishaps are the main barriers in the production industry, but the approach of TPM will be helpful for the companies.
Meaning of Total Productive Maintenance
Total Productive Maintenance makes the current production process and machinery efficient to avoid mistakes. “Ideal production” refers to zero issues, accidents, breakdowns, effects, and errors. TPM is a methodology to improve overall production performance and effectiveness.
Is TPM Necessary for Today’s Manufacturing Firms?
Some firms doubt the necessity of this methodology for manufacturing firms. Still, TPM is indeed required to reduce unplanned maintenance time and create a safer working environment for the employees.
Lean Production –Notion of Every Single Organization
The term “lean production” is very simple to read but difficult to achieve for any organization due to unavoidable situations. Hence, every production professional is trying to improve the possibilities of lean production, but it is only possible with modern approaches. This notion can be achievable by applying the Total Productive Maintenance channel.
From these points, let’s check out “how TPM helps a lot in lean production.”
1). Improve OEE By Reducing Unplanned Downtime:
The first thing you need to know here for the lean production goals is to enhance the organization’s OEE or Overall Equipment Effectiveness rates. Overall, equipment effectiveness is quite impossible for the firm without reducing the unplanned downtime. If the downtime is zero, the OEE rate will automatically improve in the company. TPM works on the same approach.
Why is it important?
OEE is the basic function every organization needs to avoid the time-wastage due to unplanned downtime. Due to the frequent drastic downtime changes, we have seen the robust method of Total Productive Maintenance in the last few years.
2). 4 Basic Principles of TPM:
This methodology is impressive for 21st-century organizations. A perfect production goal is not possible without taking care of machinery maintenance.
No Defects
No Slow Running
No Breakdown
No Accidents
All these four pillars are robust to achieve the improved production objective for an organization.
Importance of these four principles:
These four principles are not only the principle of this method but also the major pillars. Production professionals can also study comprehensively to deal with these four things during the Green Belt Training program.
3). Safer Working Environment and Culture:
Next is the most important benefit of this model. A workspace environment and culture must be safer for the employees. The TPM model makes this process easier. Clean, standardized, scheduled, and sorted workspaces create a safer work culture environment.
Why is it important?
A safer working atmosphere is not a plus point for the employees but also for the organization to avoid unnecessary expenses and less productivity.
4). Reduction in Customer Complaints:
Lean production is a long path that is not achievable without solving customer complaints. If any organization gets day-to-day customer complaints, most of the time will be devoted to solving these queries through company resources. Total Productive Maintenance reduces the rate of customer complaints to achieve enhanced production goals.
Why is it important?
Customers are the company’s assets, and to make the chain of customers credible and loyal to your business; you need to work on the reduction rate of clients’ complaints by using the approach of TPM.
5). Less Workspace Accidents:
The most important advantage of TPM is reducing workspace accidents. Nowadays, many organizations face huge losses just because of sudden workspace accidents, and sometimes it also becomes the reason for the company to shut down. With fewer workspace accidents, total production costs will be reduced, and company output will increase.
Why is it important?
A company must be well-prepared and plan for workspace accidents, but these accidents’ probability can become zero when the production managers use the TPM method.
6). Enhance Quality Output:
Zero breakdowns and zero defects are crucial to enhance the quality output. The approach of Total Productive Maintenance (TPM) is making this task into reality. TPM is not a new concept in the market, but this holistic approach was a traditional concept with modern ideas.
Why is it important?
A company should never compromise on the quality of production to life in the industry for a long-lasting time. TPM is not only for the production and manufacturing issues but also enhances the quality output.
7). Availability:
TPM’s approach makes the availability task easier and hassle-free with no-stops goals. Yes, this approach is also worthy of the Availability of the units. This approach is holistic, and that’s why it works to accomplish all major goals of organizations.
Why is it important?
Maintaining enough products for the upcoming business demand is the most important task for production managers. Even this concept is also included in the Green Belt Training certification.
The Bottom Line:
The goal of perfect production and productive maintenance can become the ride of a roller-coaster for the companies and production engineers. Still, when they work on TPM’s modern and holistic approach, everything will be easier for them. We hope this justification of TPM for the lean production goals. The approach of TPM not only empowers employees but is also helpful in accomplishing the goals of manufacturing firms. Finally, we can say that TPM is the approach to improve the quality, reduction in downtime time, improve the working atmosphere, and, most important, the ROI of the firm. TPM has now become a vital element for successful production goals.