Tata Motors digitises its manufacturing ecosystem: Latest News of 2022
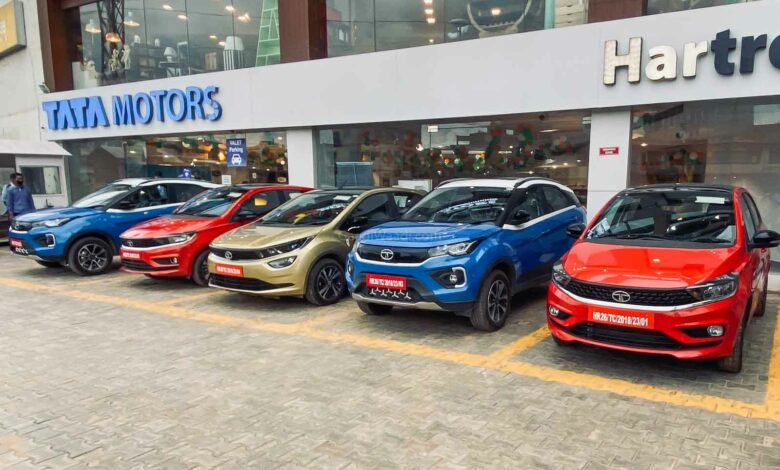
Tata Motors’ CIO, Gopinath Jayaraj, has shared how the automobile manufacturer is expanding its industry 4.0 across its seven manufacturing units in India.
In addition, he has thrown light on how the large organization manages to incorporate a digital focussed mindset among the employees.
During the last few years, manufacturing companies have enhanced their efforts in implementing various digital transformation initiatives to eradicate their competitors. The different approaches used by the manufacturers involve improving efficiency to increase workforce productivity and gain better insights safely.
Among the other manufacturing companies, one of the crucial ongoing digital transformation projects has taken within Tata Motors. The company has adopted the digitalization of the manufacturing ecosystem.
The company is one of the largest automobile manufacturers in India. Currently, they are identifying areas where digital interventions would decrease the cycle time and improve data visibility, thus improving the overall efficiency. This would also enhance the quality and safety aspects of the manufacturing process.
What are the four major approaches adopted by Tata Motors to leverage Industry 4.0:
1. Data Integration:
Tata Motors is currently looking for real-time data integration for tracking the material and processing parameters.
The closer the company will be to achieving the parameters in real-time, the swifter will be the manufacturing process of the company.
2. Identification and capture of the processed data:
The manufacturing company is also looking for ways of identifying and capturing quality, safety, and analysis of data at different levels of the manufacturing ecosystem.
Gopinath Jayaraj, CIO of Tata Motors, has revealed that this step would allow them to put light on what the fact is today and how they will know if the interventions are yielding any actual improvements in both quality and safety on the ground.
Throughput is the output of the real-time data.
3. Leveraging insights:
Tata motors are currently correlating the data between manufacturing and logistics- involving both inbound and outbound processes. These insights help in making proper decisions on the scheduling and the sequencing process.
In addition, integrating data between the firm’s HR and manufacturing also enables better human capital planning.
Cross function; integration of data is another focus area that has been driving a lot of internal efficiencies and improvements in quality.
4. Data Security:
In addition to providing attention to the following aspects, Tata Motors is currently focussing on building a high data security foundation.
Jayaraj reveals that this is one of the most challenging fields to address in the manufacturing process. People in the industry are usually known for the fact that the industries are often set up in remote locations and are required to be operational in all kinds of conditions.
Thus, the most challenging factor is to enable connectivity and secure connections with no breach possibilities. That’s one of the core things that Tata Motors is currently focussing on.
Tata Motors operates seven manufacturing plants within India, and all the locations are adopting an Industry 4.0 initiative.
The four approaches have been driven in different levels of initiatives across all locations.
Some of the initiatives are at higher levels of maturity and have been deployed in all the plants within India. Others are at different levels of maturity when they are yet to be proven. Jayaraj has said that this is an ongoing process.
Tata Motors is India’s largest automobile manufacturer, which was established in 1945. Currently, it has a revenue of Rs 2.82 lakh crores and more than 75,000 employees engaged in the sector.
During the Covid-19 pandemic, the IT sector played an integral part in enabling Tata Motor’s workforce to work remotely. This task was carried out through the enabling of network lines, VPNs, and laptops.
While the continuity of the business was ensured by making investments in the IT infrastructure, the changes have resulted in a cultural shift within the manufacturing space.
On being asked about the challenges, Jayaraj responded, saying that it was always a challenge in the manufacturing industry to introduce things like flexible timings or remote workings. The pandemic has allowed the HR team to resort to new ways of operating.
Post-pandemic, the digitalization benefits became much more systematized as a part of the organization.
The process and approach to employee engagement, workforce productivity, and measurement systems have adopted new ways of working. The HR team has shown enthusiasm for adopting digital means to drive cultural transformation.
Tata motors have been driving an employee digitalization program of employee processes for the last two years. They have designed their company’s digital platform that is linked with the company’s core HR systems. But, the approaches are completely based on the cloud and mobile native and bring the HR service to the employees.
Furthermore, Tata Motors is even using MS Teams as a medium to deploy employee processes. The company has enabled a chatbot system to book leaves and access policy documents that were launched because of the asynchronous conversations between the employees and the HRs.
The changes are interesting because they were first initiated as a response to the covid-19 pandemic. But, the system has proved to be more engaging and productive for companies through the utilization of digital technologies.
While Tata Motors is transforming its enterprise architecture into a modern digital platform, this has also enabled the changing of the mindset of the employees by creating awareness around the impact of digital systems that are making enterprise processes both internal and external.
Tata Motors HR Team is conducting awareness programs across the company to ensure that everyone is capable of understanding the kind of digital capabilities the organization already has that could be leveraged.
He emphasized that the employees need to understand what the technologies are capable of and how they can further leverage them.
The organization has a systematic program that helps to understand how technology training programs need to happen, how the workforce can be trained internally, and how can the hiring process be efficient for bringing in niche specialization.
Jayaraj has stated that the company has had its internal program called Sparks IT that they have been operating internally to increase the capability and the capacity quotient for developing the company digitally.
Edited by Prakriti Arora